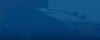
ORBITAL WELDING

ORBITAL
.png)
Your Orbital Welding Specialists
OTG provides nationwide service and support, specializing in AMI equipment repair. With repair depots in Tucson, AZ; Shrewsbury, PA; and Boise, ID, CSI offers a unique geographic footprint and ISO 9001:2015 certification. For over 10 years, we’ve implemented rigorous quality processes, becoming a leader in equipment inventory services. With 50+ years of combined orbital repair expertise, our facilities deliver reliable, high-quality service and support, making CSI the trusted choice for equipment repair across the United States.
.png)
Orbital Services FAQs
Yes, each of our shops across the United States is fully staffed with repair technicians trained to repair, maintain, and in some cases upgrade Arc Machines orbital weld heads and power supplies in addition to Tri Tool facing tools.
Most of the time this requires the trim pot needing an adjustment. If the machine indicates the weld head is too fast, you would turn the trim pot counterclockwise, and if it was indicating too slow, you would turn the trim pot clockwise. This would be the starting point to determine if the weld head needs an adjustment. There are other possibilities that could cause the weld head to be out of calibration range, like a broken wire.
-
CSI stocks common sized Arc Machines compatible precut tungsten.
-
CSI also stocks common sized collets for Arc Machines orbital weld heads.
-
We have multiple sizes of facing blades including Tri Tool durabit -1s.
-
Yes, you can call CSI and speak to a technician for technical advice.
CSI has 3 facilities. Boise, ID, Tucson, AZ, and Shrewsbury PA.
What setting for a 9-7500 weld head?
-
For an Arc Machines 9-500 weld head you would use the 20 RPM setting.
-
For an Arc Machines 9-7500 weld head you would use the 2 RMP setting.
-
The cause will likely be the plate on the power switch is not on the correct side for the amount of power you have plugged in to the outlet. 110V or 220V
The cause could be a few things:
-
First check the connections making sure all of the quick disconnects are plugged in properly.
-
Check the tungsten making sure it is not damaged.
-
Check the arc gap of the tungsten and adjust properly.
-
For “No Color Welds,” those required by some industry specifications such as a large-scale chip manufacturer or a bio-pharmaceutical application, CSI recommends a 30 second pre-purge and 30 second post-purge. This coupled with a Point of Use, Purifier (See CSI for details and recommendations), recommended for ID purge source and possible OD purge source for “ARC GAS SUPPLY,” is recommended. (CSI does supply POU, Purifiers for purchase).
Using the precut tungsten for the correct size of weld head and tube ensures the tungsten does not stick out the back of the rotor. If the tungsten does stick out of the backside of the rotor it can cause damage to the home switch which will not allow the weld head to home or calibrate correctly. Additionally, the tungsten can break off and fall into the gears damaging the gears not allowing proper welds. IF tungsten fragments or “weld spatter” drop into the gear system of the weld head, you will most likely observe a “clicking sound” when the rotor reaches a common position during rotation. Should this occur, please STOP all work the head will need to be serviced by a trained technician. Continuing to use the item could cause more damage.
-
Check home-pin for damage: The tungsten could have been installed incorrectly and hit and damaged the home-pin.
-
Home switch might need adjustment.
-
The Amphenol / motor cable wires can have a short or have been pulled out of the connector.
-
There could be tungsten or some beads inside of the gears causing the insulating coupler to break or damage to the gears causing a wobble or potential binding of the gears.
-
Your purge gas may be too high causing the weld to wander or meander.
-
Welding dissimilar materials which can include different alloys or even various blends of Stainless Steel, having differing levels of Sulfur Content, in the metal itself, can cause the ARC to meander to one side or the other. Typically, the ARC will deflect to the HIGH Sulfur side of the joint. Sulfur is well known for its ability to allow Stainless Steel to “WET” or increase wettability. In this case causing the ARC to attract away from the low Sulfur side of the joint. DEFINITION: Wettability in welding refers to how well a liquid, like a molten metal or flux, spreads and adheres over a solid surface. It’s all about the ability of the molten material to flow and make a strong bond. If the Sulfur content is too low in a specific “heat” of “mill run” of Stainless Steel, the metal may lose the ability to penetrate, also causing meander and poor penetration.
-
CSI calibrations are good for one year on the date of calibration.
The tool will not move up or down or operate when pressure is applied.
-
The shear pin / roll pin is broken inside of the tool not allowing the facing tool to face correctly. This shear pin is designed to break to prevent damage to the tool when used improperly.
-
All models of Tri Tool facing tools CSI leases have the finger guards / chip guard option. The finger guards / chip guards ensure that body parts and other foreign objects are not inserted near the facing blade when the tool is being operated.
The finger guards / chip guards are there for safety reasons and we do not recommend removing them for any reason.
CSI offers a Tri Tool 576 Sever master to cut the tube and an add on squaring module that will face tube up to 6 inches.
The major difference between AMI 8 Series and AMI 9 series is the thickness of the weld head main housing assemblies. The AMI 8 series have 3 weld head sizes, whereas the AMI 9 series have 8 weld head sizes. The AMI 8 series have a thinner main housing assembly compared to the AMI 9 series. The AMI 9 series weld head housing assembly size increases model to model as the tube size welding ability increases. While the AMI 8 series housing assembly size does not change per model.
CSI can offer equipment familiarization training but does not have an orbital welder certification program at this time.
Depending on parts’ availability, CSI aims for a 2-week turnaround on repairs.
If a piece of equipment breaks while on rent, CSI will ship out a replacement piece of equipment right away to help keep your project on schedule. The customer will ship back the broken item to the closest CSI orbital repair shop.